2023 Broiler Project with Heat Recovery - England
In the 2022, JF McKenna began work on a new six house poultry site in the UK with Clarke Group Construction, for Moy Park.
This ‘Farm of the Future’ was built with sustainability in mind, with Moy Park stating that it was so efficient, the farm would essentially operate ‘off-grid’ when all systems were operating at capacity.
After four years in the planning, birds were first placed in March 2023 and is now fully stocked with 300,000 broilers.
Stephen Beagan, head of agri-estates at Moy Park has said that Beech farm in Lincolnshire can reduce Scope 1 and Scope 2 emissions by 100%, effectively taking the farm ‘off grid’ when all systems are operating at capacity.
“We spent almost two years looking at different technologies, speaking with companies, and when we had decided what we wanted to do, we started construction in March 2022, and the build took a year, so birds were placed in March 2023.
“Sustainability is a key pillar for our business and this is the cumulation of our experience of many years across the business,” he adds. The construction company and contractor for the build was Clarke Group. The equipment was supplied by poultry specialist JF McKenna.
Technologies used on the farm to reach net-zero emissions include ground source heat pumps to generate heating, heat exchanger systems to reduce overall heat usage, and solar technology capable of generating an impressive 1MW of electricity, which will work in tandem with lithium battery storage.
“I believe most people will have heard of the technologies, but we looked at how we could use the technology to work altogether. We used a ground up approach,” he says. “We wanted to look at how to minimise energy usage, so we looked at how much heat we required and how to minimise that.
“Then we had to look at how we provided the heat we do require. We looked at many systems and decided on ground source heat. Next was how do we power that? The fuel we use is electricity so installing solar was our next step. But the sun doesn’t shine at night so we needed a battery system. So, rather than single technologies, but looked at how does technology work together.
“Everything from the design and layout of the farm building to how we capture and recycle rainwater reflects our mantra of ‘reduce, reuse, renewable,” he says. “Beech farm is a first for the poultry sector – through well thought out innovations, we have created an incredible 100% reduction in energy related GHG emissions – that represents a saving of 900 tonnes of CO2 a year. This is set to be a game-changer for the industry, particularly when taken in partnership with our other Scope 3 initiatives.”
While the systems are capable of operating at capacity full time, the farm also has back up systems in place in the case of extreme bad weather in the winter. “We don’t feel we would need them, but they are for bird welfare,” says Beagan.
“With any project on this scale there is a lot of project management,” says Beagan. “Once we had agreed the spec and design, the guys were very good. They removed what could have been a massive headache.”
Moy Park said it planned to use Beech farm as a blueprint on its journey to reach net-zero. It sources poultry from 700 farms in the UK. The farm also has the latest biosecurity measures, the company said.
Beagan is keen to emphasise the opportunities presented by the new build. “Looking at removing 100% GHC emissions represents a massive step forward,” he says. “It is somewhere we can bring out farmers and partners to show them what is achievable.
“I believe it is a milestone not only for ourselves, but also for the poultry industry. It has shown the industry what is achievable.
While he won’t discuss the cost of the farm, Beagan acknowledges it “represents a significant investment” and cost “significantly more” than a “standard farm”. However, he notes it is essential to meet our net zero aspirations.
The next stage in that journey is to monitor performance of this farm. “As we assess those technologies and see what the benefits are, we can see what can be retrofitted to other farms and consider how we do that and roll that out. “This farm will be a test bed, the blueprint. I would definitely say watch this space.”
Project Features:
Fancom Ventilation & Control system including inlets, inlet motors, chimneys, fans and individual sensors
Fancom Farm Manager Software
Fancom Bird Weighing
Chore-Time Konavi Feeding system & Augers
Lubing Drinking & Flush System
Lubing Misting System
HATO Corax lighting
Collinson Feed Bins & Fill Pipes
Collinson Tip Batch Feed Weighing
Agro Supply Heat Recovery units
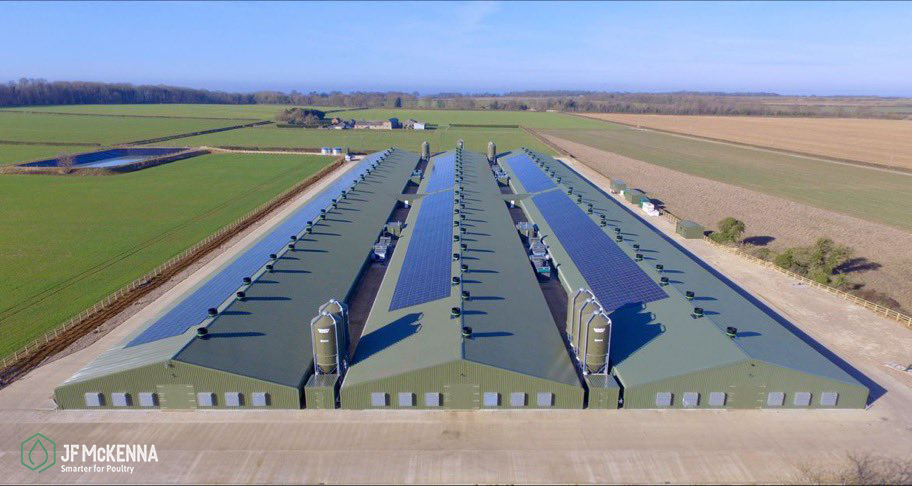
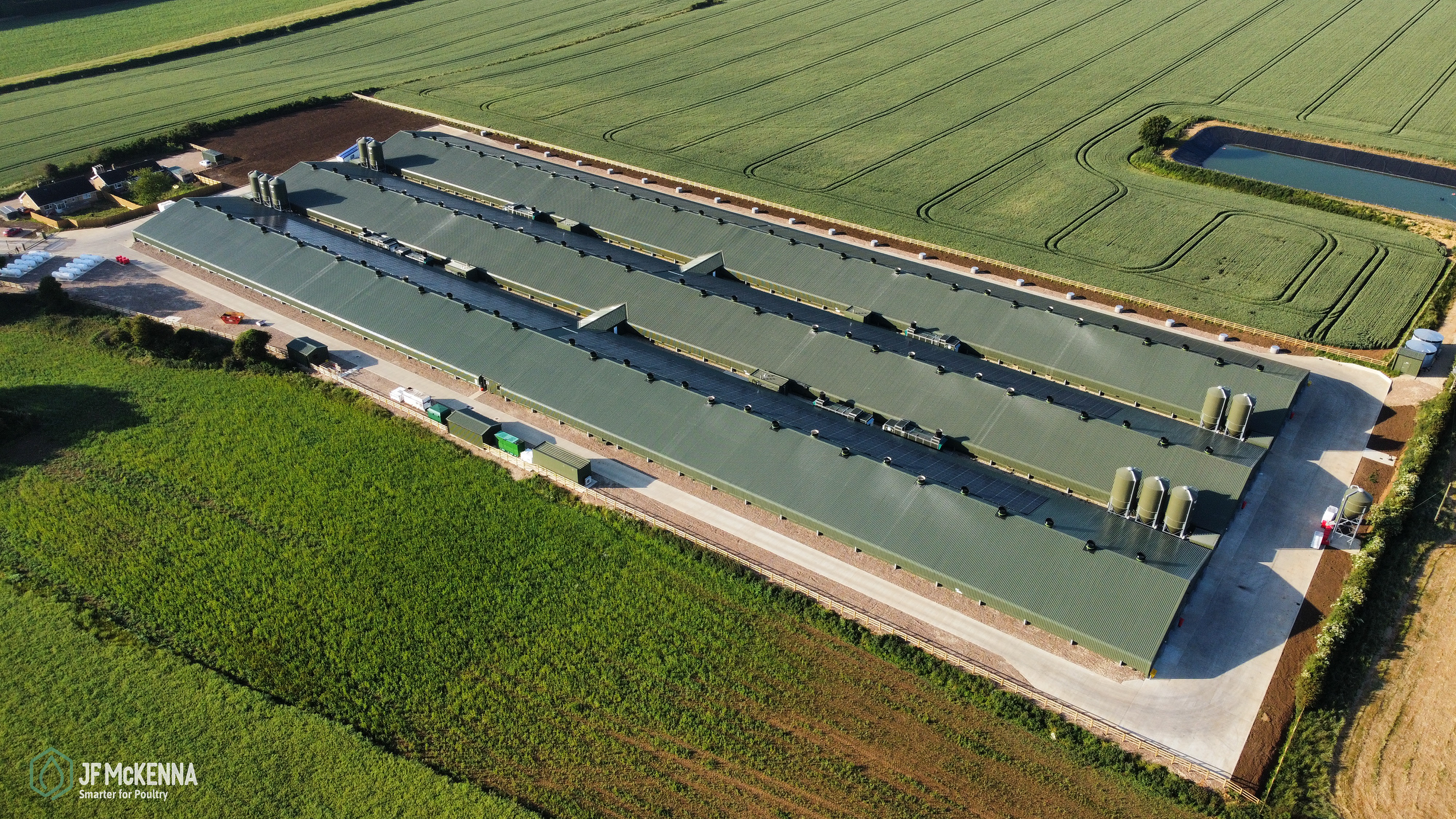
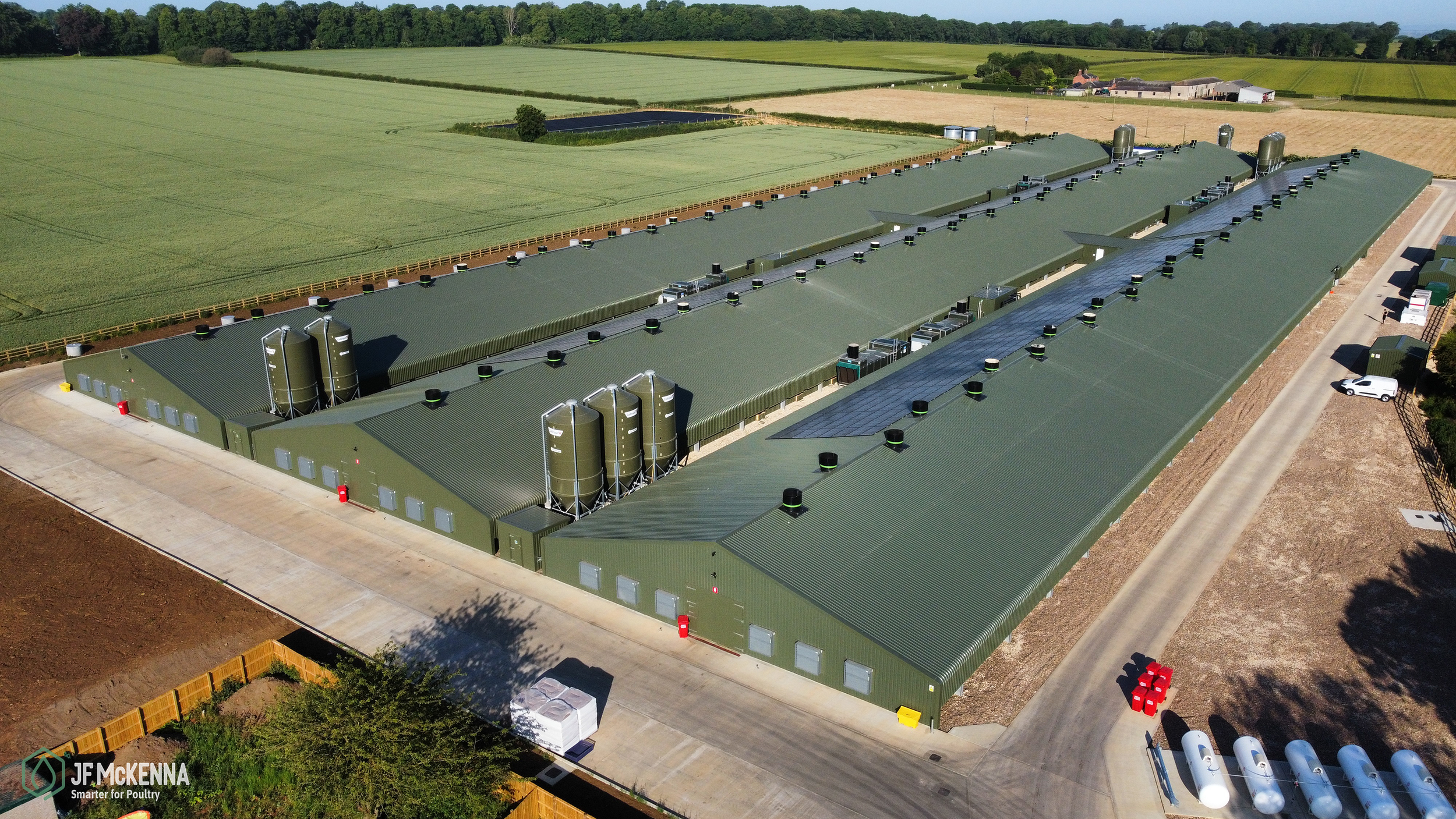
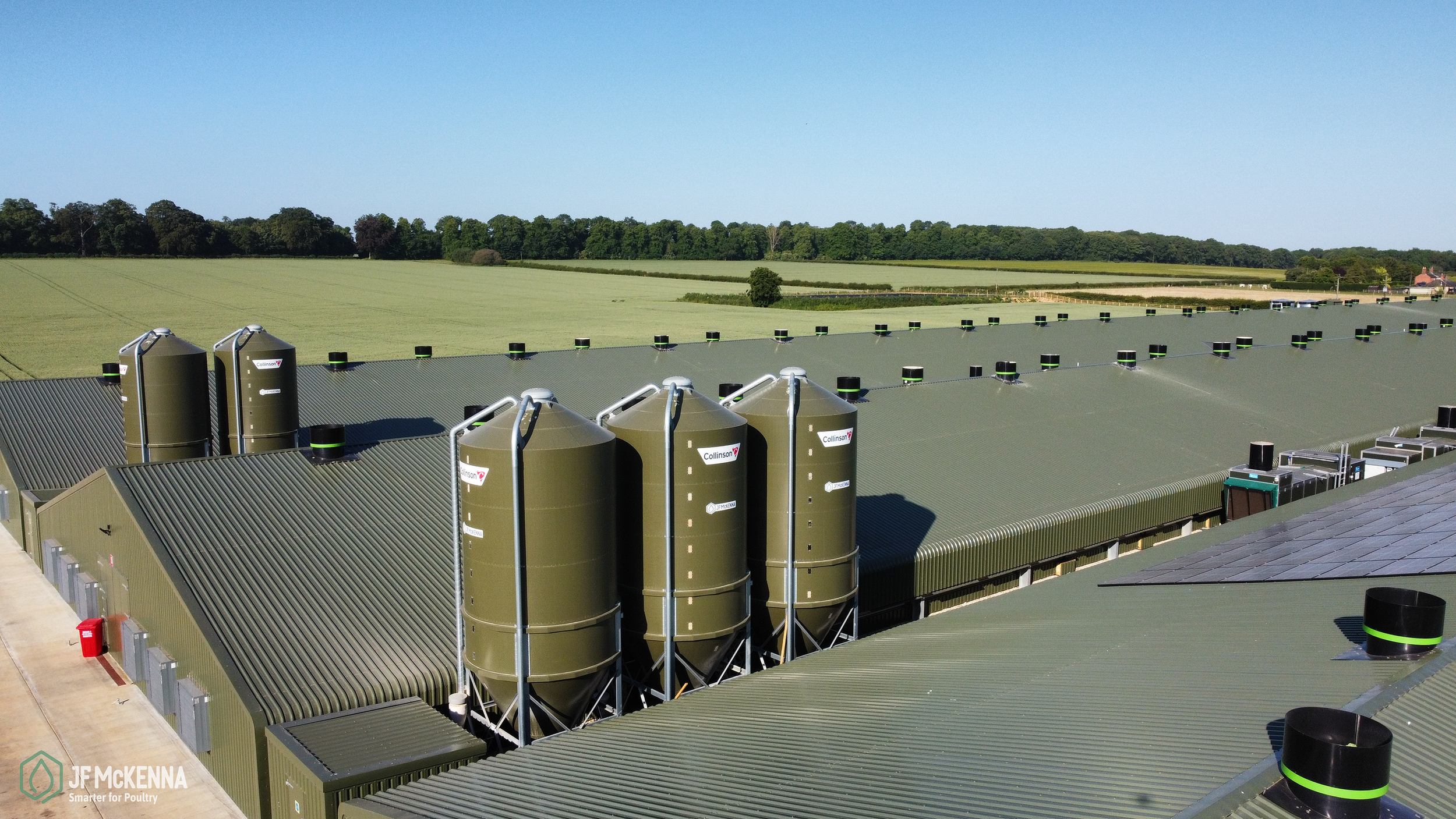